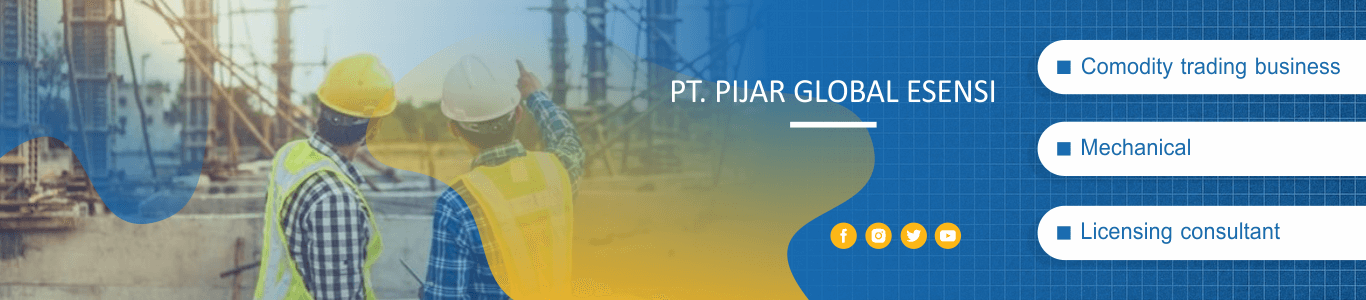
Chemical & Recycling
Traditionally, plastics recycling is undertaken using mechanical methods. Below we provide an overview of the non-mechanical recycling technologies that are currently under development in the new ‘chemical recycling’ sector.
Chemical recycling is the broad term used to describe a range of emerging technologies in the waste management industry which allow plastics to be recycled, that are difficult or uneconomic to recycle mechanically.
By turning plastic waste back into base chemicals and chemical feedstocks, chemical recycling processes have the potential to dramatically improve recycling rates and divert plastic waste from landfill or incineration.
Chemical recycling complements mechanical recycling processes by enabling the further extraction of value from polymers that have exhausted their economic potential for mechanical processing. Chemical recycling serves as an alternative to landfill and incineration for erstwhile hard-to-recycle plastic products such as films, multi-layered and laminated plastics. Additionally, chemical recycling supplies virgin-quality raw materials to the plastics supply chain. This enables the production of food grade plastics from post-consumer waste.
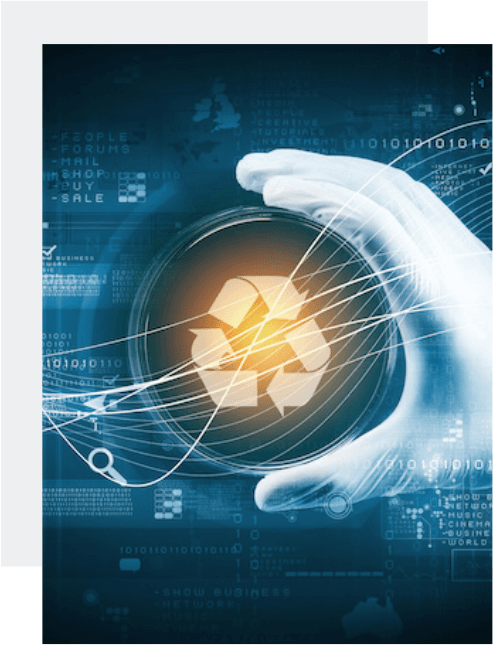
Plastic Material PET, PP & PE
1. PE
What is PE, and What is it Used For?
Polyethylene is a thermoplastic polymer with a variable crystalline structure and a vast range of applications depending on the particular type. It is one of the most widely produced plastics in the world, with tens of millions of tons produced worldwide each year. The commercial process (the Ziegler-Natta catalysts) that made PE such a success was developed in the 1950s by two scientists, Karl Ziegler of Germany and Giulio Natta of Italy.
There are several types of polyethylene, and each one is best suited for a different set of applications. Generally speaking, High-Density Polyethylene (HDPE) is much more crystalline, and is often used in entirely different circumstances than Low-Density Polyethylene (LDPE). For example, LDPE is widely used in plastic packaging, such as for grocery bags or plastic wrap. HDPE, by contrast, has common applications in construction (for example, in its use in the fabrication of drain pipes). Ultrahigh Molecular Weight Polyethylene (UHMW) has high-performance applications in things such as medical devices and bulletproof vests.
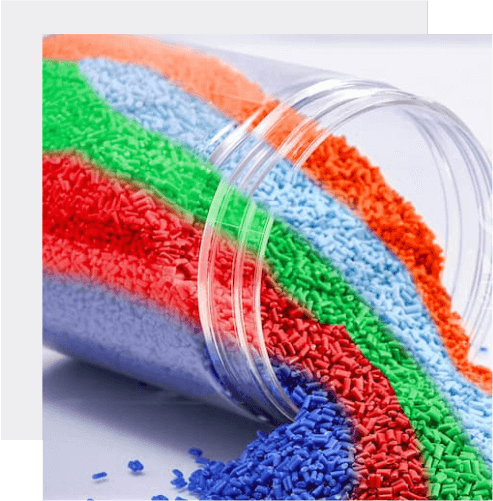
3. PP
what is PP ?Polypropylene (PP) is a tough, rigid, and crystalline thermoplastic. It is made from propene (or propylene) monomer. This linear hydrocarbon resin is the lightest polymer among all commodity plastics. PP comes either as homopolymer or as copolymer and can be greatly boosted with additives.
PP has become a material of choice, especially when you are looking for a polymer with superior strength (e.g., vs Polyamide) in engineering applications or simply looking for cost advantage in blow molding bottles (vs. PET).
How PP differs from PE?
PE and PP offer a lot of similarities which makes it easy to confuse the two materials. Understanding inherit benefits of each can help you pick the perfect material.
They both are highly malleable and have relatively similar impact resistance, meaning strength does not have to be a concern when these plastics are in use. Density is another key factor that differentiates PE from PP. Polypropylene’s density is fixed and only varies when it is filled. On the other hand, polyethylene grade selection is highly dependent on density due to different variations (Low, Medium, High). High Density Polyethylene is known for its big strength-to-density ratio, and it can be more rigid versus PP.